Hogyan készülnek a nagy pontosságú alkatrészek megmunkálása
2023-09-22
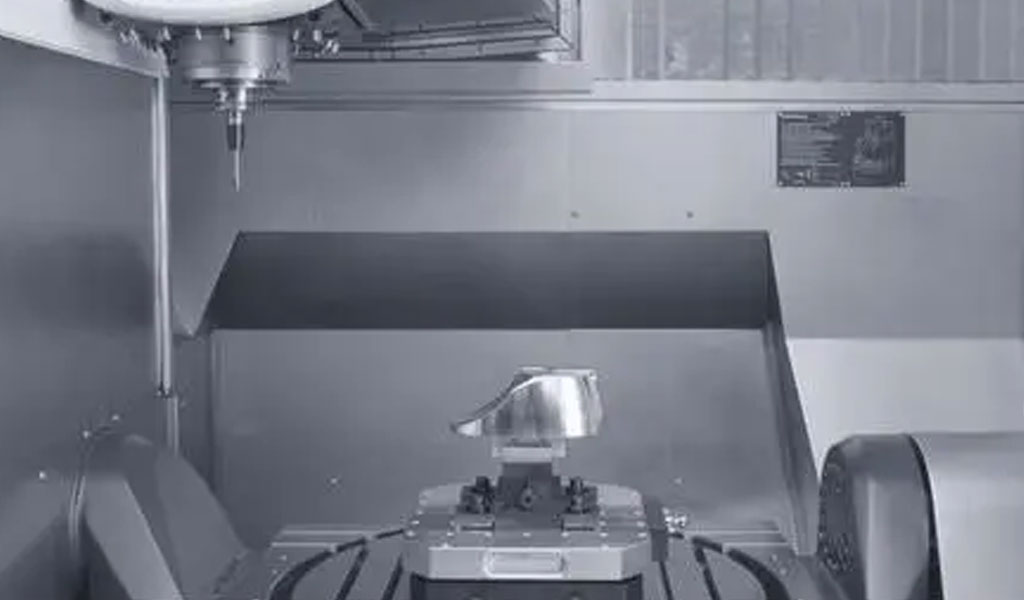
A precíziós megmunkálás megértése
A precíziós megmunkálás a modern gyártás sarokköve, amely az iparágak széles körében használt bonyolult és pontos alkatrészek előállításáért felelős. Jelentőségének teljes megértése érdekében tárjuk fel a precíziós megmunkálás alapfogalmait, a különféle ágazatokban betöltött létfontosságú szerepét, és azt a történelmi utat, amely a jelenlegi kiválósághoz vezetett.A. Mi az a precíziós megmunkálás?
A precíziós megmunkálás olyan gyártási folyamatok összességét jelenti, amelyek nagy pontossággal és irányítottsággal távolítják el az anyagot a munkadarabból, ami finoman megmunkált alkatrészeket eredményez szűk tűréssel. Ez a folyamat a nyersanyagokat, például fémeket, műanyagokat vagy kerámiákat olyan precíz alkatrészekké alakítja, amelyek megfelelnek a szigorú előírásoknak. A precíziós megmunkálás fő jellemzői a következők:- Pontosság: A precíziós megmunkálás biztosítja, hogy a végtermék pontosan megfeleljen a tervezett tervnek, minimális eltéréssel.
- Szigorú tűréshatárok: Rendkívül szűk tűréssel rendelkező alkatrészek gyártását teszi lehetővé, vagyis a kész alkatrészek pontosan megfelelnek a megadott méreteknek.
- Kiváló felületkezelés: A precíziós megmunkálás kivételes felületi minőséget biztosít, gyakran szükségtelenné téve további megmunkálási folyamatokat.
- Összetett geometriák: Bonyolult formákat, kontúrokat és jellemzőket hozhat létre, így nélkülözhetetlenné válik az összetett kialakítású alkatrészek gyártásában.
- Ismétlési: Precizitás megmunkálási folyamatEzek nagymértékben megismételhetők, biztosítva a több alkatrész egyenletes minőségét.
- Sokoldalúság: Sokféle anyagra alkalmazható, így sokféle iparágban alkalmazható.
B. A precíziós megmunkálás jelentősége
A precíziós megmunkálás óriási jelentőséggel bír számos kritikus iparágban, és hatással van mindennapi életünk különböző aspektusaira. Íme néhány nyomós ok a fontosságára:- Repülőipar: A repülőgépiparban a precíziós megmunkálás nélkülözhetetlen az extrém körülményeknek ellenálló alkatrészek elkészítéséhez. Repülőgép motorok, leszállás fogaskerék, és a szerkezeti elemek precíziósan megmunkált alkatrészekre támaszkodnak a biztonság és a teljesítmény érdekében.
- Orvosi eszközök: Az olyan orvosi eszközök, mint a sebészeti műszerek, protézisek és beültethető eszközök, precíziós megmunkálást igényelnek a biológiai kompatibilitás, a pontosság és a betegbiztonság érdekében.
- Autóipari szektor: A precíziós megmunkálású alkatrészek elengedhetetlenek az autóipar számára a járművek megbízhatóságának és hatékonyságának biztosítása érdekében. Az olyan alkatrészek, mint a motoralkatrészek, a sebességváltó rendszerek és a fékmechanizmusok precíz megmunkáláson alapulnak.
- Elektronika és félvezetők: A precíziós megmunkálás kulcsfontosságú a mikroelektronikai alkatrészek és félvezető eszközök gyártásában, ahol a csekély tűrések elengedhetetlenek a működőképességhez.
- Energiaszektor: Az energiaipar a precíziós megmunkálásra támaszkodik az energiatermelésben használt kritikus alkatrészek, köztük a turbinák, generátorok és erőátviteli alkatrészek előállításához.
- Szerszám- és szerszámkészítés: A precíziós megmunkálás kulcsfontosságú a szerszámok és matricák gyártásában, amelyeket viszont számtalan más termék előállítására használnak.
- Consumer Electronics: Az okostelefonok, laptopok és egyéb szórakoztató elektronikai cikkek gyártása során előnyt jelent a precíziós megmunkálás, amely biztosítja az elegáns kialakítást és az optimális funkcionalitást.
- Kutatás és fejlesztés: A kutatók és tudósok a precíziós megmunkálású alkatrészektől függenek a kísérletekhez, a prototípusokhoz és a laboratóriumi berendezésekhez.
C. Történelmi perspektíva
A precíziós megmunkálás útja az ókori civilizációkig nyúlik vissza, ahol a képzett kézművesek kezdetleges eszközöket használtak az anyagok formálására. Az akkoriban elért pontosság azonban korlátozott volt a korabeli szabványokhoz képest.- Korai precíziós megmunkálás: A 18. és 19. századi ipari forradalom meghatározó időszakot jelentett a precíziós megmunkálás fejlődésében. A szerszámgépek, például az eszterga- és marógépek feltalálása forradalmasította a gyártást azáltal, hogy nagyobb pontosságot és következetességet tett lehetővé.
- A második világháború: A precíziós megmunkálásnak meghatározó szerepe volt a második világháborúban, hiszen elengedhetetlen volt a katonai felszerelések megkívánt precizitással és egységességgel történő előállításához. Ez a korszak a megmunkálási technikák fejlődésének és új anyagok megjelenésének volt tanúja.
- A háború utáni haladás: A háború utáni időszakban felpörögtek a technológiai újítások, beleértve a számítógépes numerikus vezérlésű (CNC) gépek használatát. CNC megmunkálás lehetővé tette az automatizált és rendkívül precíz műveleteket, ami a gyártás új korszakát nyitja meg.
- A digitális korszak: A számítógépek és szoftverek integrálása a megmunkálási folyamatokba tovább emelte a precíziós megmunkálást. A modern CNC gépek páratlan pontossággal képesek bonyolult műveleteket végrehajtani, így nélkülözhetetlenek a mai gyártási környezetben.
Anyagok és jelentőségük
Az anyagok jelentik a precíziós megmunkálás alapját, a megfelelő anyag kiválasztása pedig döntő szerepet játszik a nagy pontosságú alkatrészek gyártásában. Ebben a részben elmélyülünk a megfelelő anyagok kiválasztásának fontosságában, megértjük az anyagtulajdonságok jelentőségét, és feltárjuk a megmunkálhatóságot befolyásoló különféle tényezőket.A. Anyagok kiválasztása
Az anyagok kiválasztása a precíziós megmunkálás során kritikus döntés, amely közvetlenül befolyásolja a végtermék teljesítményét, tartósságát és funkcionalitását. Az anyagok kiválasztásakor a gyártóknak több tényezőt is figyelembe kell venniük:- Anyagmegfelelőség: Az anyagnak alkalmasnak kell lennie a tervezett alkalmazásra. A különböző iparágak és alkalmazások eltérő követelményeket támasztanak, mint például a hőmérséklet-állóság, a korrózióállóság és az elektromos vezetőképesség.
- Mechanikai tulajdonságok: A mechanikai tulajdonságok, például a szakítószilárdság, a keménység és a hajlékonyság kulcsfontosságúak. Például a repülésben a nagy szakítószilárdságú anyagokat részesítik előnyben szerkezeti elemekként.
- Termikus tulajdonságok: Egyes alkalmazásokhoz kiváló hővezető képességű vagy magas hőmérsékletnek ellenálló anyagokra van szükség. Ez különösen fontos az olyan iparágakban, mint az energiatermelés és az elektronika.
- Korróziós ellenállás: Olyan környezetben, ahol a korrózió aggodalomra ad okot, előnyben részesítik a nagy korrózióálló anyagokat, például rozsdamentes acélt vagy titánt.
- Súlymegfontolások: Az olyan iparágak, mint az autóipar és a repülőgépipar, gyakran előnyben részesítik a könnyű anyagokat, például az alumíniumot vagy a szénszálas kompozitokat, hogy csökkentsék az üzemanyag-fogyasztást és javítsák a teljesítményt.
- Költségkorlátozások: A költség jelentős tényező az anyagválasztásban. A nagy teljesítményű anyagok drágák lehetnek, ezért a gyártóknak egyensúlyt kell találniuk a teljesítmény és a költséghatékonyság között.
- Előírásoknak való megfelelés: Az olyan iparágakban, mint az egészségügy, az anyagoknak meg kell felelniük a szigorú biokompatibilitási és biztonsági előírásoknak.
- Elérhetőség: Az anyagok elérhetősége és forrásai is befolyásolják a kiválasztást. Egyes speciális ötvözetek vagy kompozitok korlátozottan állnak rendelkezésre.
B. Anyagtulajdonságok
Az anyagok tulajdonságainak megértése kulcsfontosságú a precíziós megmunkáláshoz. Íme néhány lényeges anyagtulajdonság és azok jelentősége:- Szakítószilárdság: A szakítószilárdság azt méri, hogy az anyag mennyire képes ellenállni a húzóerőnek törés nélkül. Elengedhetetlen a szerkezeti elemekhez és a mechanikai igénybevételnek kitett alkatrészekhez.
- Keménység: A keménység az anyag deformációval és kopással szembeni ellenállását jelzi. A kemény anyagok alkalmasak vágószerszámokhoz, míg a lágyabb anyagok bizonyos alkalmazásokhoz, például tömítésekhez előnyösek.
- Hajlékonyság: A hajlékonyság az anyag azon képességére utal, hogy szakadás nélkül deformálódik, ha húzófeszültségnek van kitéve. A képlékeny anyagok könnyebben alakíthatók, de előfordulhat, hogy nem alkalmasak merevséget igénylő alkalmazásokhoz.
- Hővezető: A nagy hővezető képességű anyagok hatékonyan vezetik el a hőt. Ez a tulajdonság létfontosságú olyan alkalmazásokban, ahol kritikus a hőmérséklet-szabályozás.
- Elektromos vezetőképesség: Az elektromos vezetőképesség elengedhetetlen az elektronikában és az elektromos alkatrészekben, ahol az anyagoknak elő kell segíteniük az elektromos áram áramlását.
- Mágneses tulajdonságok: A mágneses tulajdonságok jelentősek az olyan iparágakban, mint az elektromágnesesség és az elektronika, ahol az anyagoknak ferromágnesesnek vagy nem mágnesesnek kell lenniük.
- Kémiai ellenállás: Az anyagoknak ellenállniuk kell a kémiai korróziónak olyan környezetben, ahol savaknak, lúgoknak vagy más korrozív anyagoknak vannak kitéve.
C. Megmunkálhatósági tényezők
A megmunkálhatóság az anyag megmunkálásának, vágásának vagy formázásának egyszerűségére utal. Számos tényező befolyásolja, többek között:- Anyagkeménység: A lágyabb anyagokat általában könnyebb megmunkálni, míg a keményebb anyagokhoz speciális szerszámok és technikák szükségesek.
- Forgácsképződés: A forgácsok képződése és kiürítése a megmunkálás során befolyásolja a folyamat hatékonyságát és felületi minőségét.
- Szerszámkopás: A különböző anyagok különböző mértékű szerszámkopást okozhatnak, ami befolyásolja a megmunkálási sebességet és a költségeket.
- Hűtőfolyadék és kenés: A megfelelő hűtőfolyadék és kenés elengedhetetlen a súrlódás, a hő és a szerszámkopás csökkentéséhez a megmunkálás során.
- Vágási sebesség: Az a sebesség, amellyel a vágószerszám áthalad az anyagon, hatással van a termelékenységre és a megmunkált felület minőségére is.
- Szerszám Anyaga: A vágószerszám anyagának kiválasztása, például keményfém vagy gyorsacél, a megmunkált anyagtól függ.
- Vágási paraméterek: A forgácsolási paraméterek, például az előtolás és a fogásmélység beállításával optimalizálható a megmunkálási folyamat bizonyos anyagokhoz.
Szerszámgépek precíziós megmunkáláshoz
A szerszámgépek a precíziós megmunkálás szíve, lehetővé téve a nyersanyagok nagy pontosságú alkatrészekké történő átalakítását. Ebben a részben a precíziós megmunkálásban használt szerszámgépek négy fő típusát vizsgáljuk meg: CNC megmunkáló központokat, esztergagépeket, köszörűgépeket és EDM-et (elektromos kisülési megmunkálás). Ezen gépek mindegyike egyedülálló szerepet tölt be a precíz alkatrészek gyártásában.A. CNC megmunkáló központok
A CNC (Computer Numerical Control) megmunkálóközpontok sokoldalúak és széles körben használatosak a precíziós megmunkálásban. Ezek olyan automatizált rendszerek, amelyek kivételes pontossággal szabályozzák a vágószerszámok és a munkadarabok mozgását. Íme egy áttekintés a CNC megmunkáló központokról és jelentőségükről:- Sokoldalúság: A CNC megmunkáló központok különféle megmunkálási műveleteket végezhetnek, beleértve a marást, fúrást és menetfúrást. Ez a sokoldalúság lehetővé teszi összetett alkatrészek gyártását több funkcióval.
- Nagy pontosságú: A CNC gépek számítógépes vezérlése precíz szerszámpozícionálást és konzisztens eredményt biztosít, így ideálisak szűk tűréssel rendelkező alkatrészekhez.
- Automatizálás: A CNC megmunkáló központok folyamatosan, minimális emberi beavatkozással működhetnek. Ez az automatizálás növeli a hatékonyságot és csökkenti a hibák kockázatát.
- Összetett geometriák: Kiemelkednek a bonyolult formák és kontúrok megmunkálásában, így alkalmasak olyan iparágakban, mint a repülőgépipar, ahol gyakoriak az összetett alkatrészek.
- Megismételhető eredmények: A CNC gépek kiváló ismételhetőséget kínálnak, biztosítva, hogy minden gyártott alkatrész megfeleljen a tervezés pontos specifikációinak.
- Csökkentett beállítási idő: A CNC megmunkáló központok programozhatók a különböző feladatok közötti gyors váltáshoz, minimalizálva a beállítási időt és növelve a gyártás hatékonyságát.
B. Esztergagépek
Az esztergagépeket hengeres alkatrészek létrehozására használják a munkadarab forgatásával, miközben a vágószerszám eltávolítja az anyagot a külső felületéről. A termeléshez nélkülözhetetlenek tengelys, csapok és egyéb forgásszimmetriájú alkatrészek. Az esztergagépekkel kapcsolatos legfontosabb szempontok a következők:- Hengeres alkatrészek: Az esztergagépek hengeres vagy cső alakú alkatrészek gyártására specializálódtak, beleértve a menetes vagy bonyolult hornyú alkatrészeket is.
- Nagy sebesség: Nagy sebességgel működnek, így alkalmasak olyan alkatrészekhez, amelyek sima és pontos felületet igényelnek.
- Egytengelyes működés: A legtöbb esztergagép egytengelyes, és a munkadarab külső felületének alakítására összpontosít.
- Hatékony a tömeggyártáshoz: Az esztergálás rendkívül hatékony tömeggyártású alkatrészeknél, minimális anyagveszteséggel.
- Esztergagépek: A kézi és CNC-vezérlésű esztergagépek gyakran használt esztergagépek, amelyek számos képességet kínálnak.
C. Csiszológépek
A csiszológépeket kemény vagy koptató anyagok precíziós felületkezelésére és formázására tervezték. Kulcsfontosságúak a rendkívül szűk tűréshatárok és a kiváló felületi minőség eléréséhez. Ezért fontosak a köszörűgépek:- Mikron szintű pontosság: A köszörűgépek mikron szintű pontosságot tudnak elérni, így elengedhetetlenek a legmagasabb szintű pontosságot igénylő alkalmazásokhoz.
- Anyag eltávolítása: Dörzsöléssel távolítják el az anyagot, lehetővé téve a felületi hibák kijavítását és kivételes simaság elérését.
- Szerszám és vágó köszörülés: A felületi köszörülésen kívül léteznek speciális csiszológépek a vágószerszámok élezésére és precíz profilok készítésére.
- Különféle köszörülési módszerek: Különböző típusú csiszológépek, beleértve a felületcsiszolókat, hengeres csiszolókat és középpont nélküli csiszolókat, különféle megmunkálási igényeket elégítenek ki.
- Edzett anyagok: A köszörülés különösen alkalmas edzett anyagokhoz, például szerszámacélhoz és kerámiához, ahol a hagyományos megmunkálási módszerek hatástalanok lehetnek.
D. EDM (elektromos kisüléses megmunkálás)
Az EDM vagy elektromos kisülési megmunkálás egy nem hagyományos megmunkálási eljárás, amely elektromos kisüléseket használ az anyagok formálására. Ideális bonyolult és kényes alkatrészek készítéséhez, ahol a hagyományos vágószerszámok kárt okozhatnak. Az EDM legfontosabb szempontjai a következők:- Nincs fizikai érintkezés: Az EDM nem jár közvetlen fizikai érintkezéssel a szerszám és a munkadarab között, minimálisra csökkentve a szerszám kopásának és a törékeny anyagok károsodásának kockázatát.
- Nagy pontosságú: Nagy pontosságú és felületi minőséget érhet el, még rendkívül kemény anyagokkal is.
- Huzalos szikraforgácsolás és szikraforgácsoló szikraforgácsolás: Az EDM gépeknek két elsődleges típusa van: drótvágás EDM, amely huzalelektródát használ, és süllyesztő EDM, amely formázott elektródát használ.
- Összetett formák: Az EDM bonyolult formákat, például matricákat és formákat képes előállítani, bonyolult részletekkel és finom jellemzőkkel.
- Hőhatás övezet: Mivel az EDM nem termel hőt a munkadarabon, alkalmas hőérzékeny anyagokhoz, például repülőgép-űrötvözetekhez.
- Lassú folyamat: Az EDM viszonylag lassú a többi megmunkálási módszerhez képest, így a legalkalmasabb kis mennyiségű, nagy pontosságú munkákhoz.
Vágószerszámok és szerszámok
A vágószerszámok a precíziós megmunkálás élvonalában állnak, olyan eszközökként szolgálnak, amelyek a nyersanyagokat nagy pontosságú alkatrészekké alakítják és alakítják át. Ebben a részben feltárjuk a különféle forgácsolószerszámokat, a szerszámbevonatok fontosságát, valamint a szerszám élettartamát és kopását befolyásoló tényezőket.A. A vágószerszámok típusai
A precíziós megmunkálás a forgácsolószerszámok széles skáláján alapul, mindegyiket meghatározott feladatokhoz és anyagokhoz tervezték. A vágószerszám kiválasztása nagyban befolyásolja a megmunkálási folyamat hatékonyságát és pontosságát. Íme néhány gyakori vágószerszám típus:- End Mills: A szármarók sokoldalú szerszámok, amelyeket marási műveletekhez használnak. Több vágóélük van, és különféle módon eltávolíthatják az anyagot a munkadarabból, beleértve a homlokzatot, a kontúrozást és a hornyolást.
- Fúrók: A fúrókat lyukak készítésére tervezték a munkadarabokon. Különféle formákban kaphatók, beleértve a csavarfúrókat, a középső fúrókat és az váltófúrókat.
- Esztergagépek esztergálása: Ezeket esztergagépekben használják hengeres alkatrészek formázására. Az esztergalapkák sokféle formában és anyagból állnak rendelkezésre, hogy megfeleljenek a különböző alkalmazásoknak.
- Marók: A marók különböző formájúak, például homlokmarók, golyósmarók és horonymarók, és marógépekben használják a munkadarab különböző jellemzőinek létrehozására.
- Reamerek: A dörzsárakat a korábban fúrt lyukak pontos méretre történő kidolgozására és méretezésére használják. Sima és pontos furatfelületet biztosítanak.
- Taps and Dies: Ezeket a vágószerszámokat menetvágási műveletekhez használják. A menetfúrók belső meneteket, míg a matricák külső meneteket hoznak létre.
- Kerekek köszörülése: A csiszolókorongok precíziós felületi csiszoláshoz használt csiszolószerszámok. Különféle csiszolóanyagban és szemcseméretben kaphatók.
- Melltűk: A broaches speciális szerszámok belső és külső formák és profilok, például hornyok és hornyok vágására.
- Ellenfúrók és süllyesztők: Ezeket az eszközöket a furatok körüli mélyedések vagy letörések létrehozására használják kapocss.
- Unalmas bárok: A fúrórudakat fúrási műveleteknél használják a meglévő furatok pontos növelésére.
B. Szerszámbevonatok
A szerszámbevonatok vékony anyagrétegek, amelyeket a forgácsolószerszámokra visznek fel, hogy növeljék azok teljesítményét és tartósságát. Ezek a bevonatok számos előnnyel rendelkeznek:- Csökkentett súrlódás: Az olyan bevonatok, mint a titán-nitrid (TiN) és a titán-karbonitrid (TiCN) csökkentik a súrlódást a szerszám és a munkadarab között, ami simább vágást és hosszabb szerszámélettartamot eredményez.
- Fokozott keménység: A bevonatok növelik a szerszám felületének keménységét, így ellenállóbbá teszik a kopással és meghosszabbítják a szerszám élettartamát.
- Javított hőállóság: A bevonatok ellenállnak a megmunkálás során keletkező magas hőmérsékletnek, csökkentve a szerszám hő okozta kopását és növelve a vágási sebességet.
- Felépítést gátló tulajdonságok: Egyes bevonatok tapadásgátló tulajdonságokkal rendelkeznek, amelyek megakadályozzák az anyag felhalmozódását a szerszám vágóélein.
- Fokozott kenőképesség: A bevonatos szerszámok javított kenőképességgel rendelkeznek, csökkentve a túlzott hűtőfolyadék szükségességét és javítva a forgácselszívást.
C. Szerszám élettartama és kopása
A szerszám élettartamának és kopásának megértése alapvető fontosságú a megmunkálási folyamatok optimalizálása és a gyártási költségek minimalizálása szempontjából. A szerszám élettartama azt az időtartamot jelenti, ameddig a vágószerszám hatékony marad, mielőtt cserét vagy felújítást igényelne. Számos tényező befolyásolja a szerszám élettartamát és kopását:- Vágási sebesség: A nagyobb forgácsolási sebesség a megmunkálás során fellépő magasabb hőmérséklet miatt megnövekedett szerszámkopáshoz vezethet. A vágási sebesség megfelelő megválasztása elengedhetetlen a szerszám élettartamának és a termelékenységnek az egyensúlyához.
- Feed rate: A vágószerszámnak a munkadarabba való előrehaladásának sebessége befolyásolja a szerszám kopását. A nagy előtolás felgyorsíthatja a kopást, míg az alacsonyabb előtolás meghosszabbíthatja a szerszám élettartamát.
- A vágás mélysége: A vágásmélység befolyásolja a menetenként eltávolított anyag mennyiségét. A mélyebb vágások növelhetik a szerszámkopást, ezért a mélység optimalizálása kritikus fontosságú.
- Anyagkeménység: A kemény anyagok vágása felgyorsíthatja a szerszámkopást. A kemény anyagok hatékony megmunkálásához speciális szerszámokat és bevonatokat használnak.
- Hűtőfolyadék és kenés: A megfelelő hűtőfolyadék és kenés elősegíti a hő elvezetését és csökkenti a súrlódást, meghosszabbítva a szerszám élettartamát.
- Szerszám Anyaga: Az anyag, amelyből a vágószerszám készült, befolyásolja a kopásállóságát. Az olyan anyagok, mint a keményfém és a kerámia, kiváló kopásállóságot biztosítanak.
- Szerszámgeometria: A vágószerszám geometriája, beleértve a dőlésszöget, a domborítási szöget és a forgácstörő kialakítását, jelentős szerepet játszik a kopási mintákban.
- Munkadarab anyaga: A megmunkált anyag típusa befolyásolja a szerszám kopását. A koptató anyagok gyorsabb szerszámkopáshoz vezethetnek.
Precíziós megmunkálási folyamatok
A precíziós megmunkálási eljárások azok a módszerek, amelyek során a nyersanyagokat nagy pontosságú alkatrészekké alakítják, szűk tűréssel és kivételes felületi minőséggel. Ebben a részben öt kulcsfontosságú precíziós megmunkálási folyamatot fogunk megvizsgálni: esztergálás, marás, fúrás, köszörülés és elektromos kisüléses megmunkálás (EDM). Ezen eljárások mindegyike egyedi célt szolgál, és a munkadarab egyedi követelményei alapján alkalmazzák.A. Esztergálás
Az esztergálás olyan megmunkálási eljárás, amelyet elsősorban hengeres alkatrészek alakítására használnak. Ez magában foglalja a munkadarab elforgatását, miközben egy egypontos vágószerszám eltávolítja az anyagot a külső felületről. Íme az esztergálás legfontosabb szempontjai:- Hengeres alkatrészek: Az esztergálás ideális hengeres alkatrészek, például tengelyek, csapok és hüvelyek előállításához.
- Forgási szimmetria: Forgásszimmetriát igénylő alkatrészekhez jól használható, mivel a munkadarab esztergagépen forog, miközben a vágószerszám formálja.
- Különféle műveletek: Az esztergálás különféle műveleteket hajthat végre, beleértve a ráfordítást, az esztergálást (az átmérő csökkentése), a kúpos esztergálást és a menetvágást.
- Egypontos vágás: Egyetlen vágószerszám folyamatos mozgással távolítja el az anyagot, ami hatékony anyageltávolítást eredményez.
- Esztergagépek: Mind a kézi, mind a CNC vezérlésű esztergagépeket általában esztergálási műveletekhez használják.
B. Marás
A marás egy sokoldalú precíziós megmunkálási eljárás, amely többpontos forgácsolószerszámokat alkalmaz az anyag eltávolítására a munkadarabból. Kiválóan alkalmas sokféle forma és jellemző létrehozására. A marás fő szempontjai a következők:- Sokoldalúság: A marással sík felületek, hornyok, zsebek és összetett kontúrok hozhatók létre. 2D és 3D megmunkáláshoz egyaránt használható.
- Többpontos vágás: A szerszám több vágóéle egyidejűleg érintkezik a munkadarabbal, ami lehetővé teszi a hatékony anyageltávolítást.
- A marás típusai: A marás különféle típusú marógépekkel végezhető, beleértve a szármarót, a homlokmarót és a golyósmarót.
- CNC megmunkáló központok: A CNC vezérlésű marógépek precíz vezérlést biztosítanak a szerszámmozgás felett, és széles körben használják a modern megmunkálásban.
- Nagy sebesség: A marás nagy sebességgel végezhető, ami hatékony termelést tesz lehetővé.
C. Fúrás
A fúrás egy precíziós megmunkálási eljárás, amellyel lyukakat készítenek a munkadarabokon. Ez alapvető művelet a különböző iparágakban. A fúrás legfontosabb szempontjai a következők:- Lyuk létrehozása: A fúrógépek speciális szerszámokat, úgynevezett fúrókat használnak az anyag eltávolítására és meghatározott átmérőjű lyukak létrehozására.
- Fúrók típusai: Különböző típusú fúrók állnak rendelkezésre, beleértve a spirálfúrókat, a középső fúrókat és az váltófúrókat, amelyek mindegyike meghatározott alkalmazásokhoz készült.
- Pontosság: A precíz pozicionálás és igazítás elengedhetetlen a fúrás során, hogy a furatok pontosan készüljenek.
- Sebesség és előtolás: Az olyan fúrási paraméterek, mint a forgási sebesség és az előtolás kritikusak a kívánt furatméretek eléréséhez.
- Hűtőfolyadék és kenés: Megfelelő hűtőfolyadékot és kenést alkalmaznak a hő elvezetésére és a fúrás közbeni súrlódás csökkentésére.
D. Köszörülés
A köszörülés egy precíziós megmunkálási folyamat, amely csiszolókorongokat alkalmaz az anyag eltávolítására, valamint rendkívül szűk tűrések és felületi minőség elérésére. A csiszolás fő szempontjai a következők:- Kivételes pontosság: A köszörülés mikron szintű pontosságot érhet el, így ideális a legnagyobb pontosságot igénylő alkalmazásokhoz.
- Felület kidolgozása: Kiváló felületi minőséget produkál, gyakran szükségtelenné téve a további befejező folyamatokat.
- Anyagok: A köszörülés alkalmas kemény és koptató anyagokhoz, beleértve az edzett acélt, kerámiákat és keményfémeket.
- Különféle köszörülési módszerek: Különböző típusú csiszológépek, mint például felületcsiszolók, hengeres csiszolók és középpont nélküli csiszolók, különféle megmunkálási igényeket elégítenek ki.
- Hűtőfolyadék: A megfelelő hűtőfolyadék elengedhetetlen a csiszoláshoz a túlmelegedés megelőzése és a kerék épségének megőrzése érdekében.
E. Elektromos kisülési megmunkálás (EDM)
Az EDM vagy elektromos kisülési megmunkálás egy nem hagyományos precíziós megmunkálási eljárás, amely elektromos kisüléseket használ az anyag eltávolítására. Különösen alkalmas összetett és bonyolult formák, valamint kemény és hőálló anyagok megmunkálására. Az EDM legfontosabb szempontjai a következők:- Érintkezés nélküli megmunkálás: Az EDM nem jár közvetlen érintkezéssel a szerszám és a munkadarab között, csökkentve a szerszám kopásának és károsodásának kockázatát.
- Nagy pontosságú: Az EDM nagy pontosságot tud elérni, így alkalmas olyan alkalmazásokra, ahol elengedhetetlen a szűk tűréshatár.
- Összetett formák: Komplex formák, matricák, formák és finom részletekkel rendelkező alkatrészek megmunkálásában kiváló.
- Huzalos szikraforgácsolás és szikraforgácsoló szikraforgácsolás: A szikraforgácsoló gépeknek két elsődleges típusa van: a huzalos szikraforgácsológép, amely huzalelektródát használ, és a süllyesztő szikraforgácsolás, amely formázott elektródát használ.
- Lassú folyamat: Az EDM viszonylag lassú a többi megmunkálási módszerhez képest, így a legalkalmasabb kis mennyiségű, nagy pontosságú munkákhoz.
Tűrések és minőség-ellenőrzés
A precíziós megmunkálás megköveteli a részletekre való aprólékos odafigyelést és a minőség-ellenőrzés iránti szigorú elkötelezettséget annak biztosítása érdekében, hogy az alkatrészek megfeleljenek a meghatározott szabványoknak. Ebben a részben a precíziós megmunkálás minőség-ellenőrzésének három kritikus aspektusát vizsgáljuk meg: a geometriai méretezést és toleranciát (GD&T), a statisztikai folyamatvezérlést (SPC) és a minőségbiztosítást.A. Geometriai méretezés és tolerancia (GD&T)
A geometriai méretezés és tolerancia, amelyet gyakran GD&T-nek is szoktak rövidíteni, egy olyan rendszer, amely meghatározza és kommunikálja a megengedett eltéréseket a méretben, formában, tájolásban és a jellemzők elhelyezkedésében az alkatrészen. A GD&T létfontosságú a precíziós megmunkálásban a következő okok miatt:- Precíz kommunikáció: A GD&T szabványosított nyelvet biztosít a mérnökök, tervezők és gépészek számára a tervezési szándék és a méretkövetelmények pontos kommunikálásához.
- Tolerancia tisztázása: Segít meghatározni a kritikus dimenziók elfogadható eltérését, biztosítva, hogy minden érdekelt fél megértse a megengedett eltéréseket.
- Továbbfejlesztett minőség: A GD&T elősegíti a minőség javítását azáltal, hogy csökkenti a tervezési specifikációk kétértelműségét, minimalizálva a megmunkálás során előforduló hibák kockázatát.
- Költséghatékonyság: Az egyértelmű GD&T specifikációk csökkenthetik a gyártási költségeket, mivel kevésbé valószínű, hogy az alkatrészeket félreértés vagy félreértelmezés miatt selejtezzük, vagy utómunkálást igényelnek.
- Komplex geometria: Különösen hasznos összetett geometriájú alkatrészek esetén, biztosítva, hogy minden jellemző a kívánt specifikáció szerint készüljön.
B. Statisztikai folyamatvezérlés (SPC)
A Statistical Process Control (SPC) egy minőség-ellenőrzési módszertan, amely statisztikai technikákat használ a megmunkálási folyamat figyelésére és vezérlésére. Az SPC elengedhetetlen a precíziós megmunkálásban a következő okok miatt:- Folyamatfigyelés: Az SPC segít a megmunkálási folyamatok valós idejű nyomon követésében, azonosítva a kívánt paraméterektől való eltéréseket vagy eltéréseket.
- A problémák korai felismerése: A folyamat folyamatos figyelemmel kísérésével az SPC lehetővé teszi az olyan problémák korai felismerését, amelyek nem megfelelő alkatrészekhez vezethetnek, csökkentve a hulladékot és az utómunkálatokat.
- Adatvezérelt döntéshozatal: Az SPC adatokra és statisztikai elemzésekre támaszkodik, hogy megalapozott döntéseket hozzon a folyamatbeállításokról, biztosítva, hogy a megmunkálási folyamat az elfogadható határokon belül maradjon.
- Továbbfejlesztett konzisztencia: Az SPC elősegíti a folyamat konzisztenciáját és csökkenti a nem megfelelő alkatrészek előállításának valószínűségét.
- Csökkentett selejt és átdolgozás: A folyamateltérések azonnali azonosításával és kezelésével az SPC minimalizálja a hibás alkatrészek gyártását, csökkentve a selejtezési és utómunkálati költségeket.
C. Minőségbiztosítás a precíziós megmunkálásban
A precíziós megmunkálás minőségbiztosítása átfogó megközelítést foglal magában annak biztosítására, hogy a gyártott alkatrészek megfeleljenek vagy meghaladják a meghatározott minőségi szabványokat. Különféle elemeket foglal magában, többek között:- Folyamat dokumentációja: A megmunkálási folyamatok részletes dokumentációja, beleértve a szabványos működési eljárásokat (SOP) és a munkautasításokat is, biztosítja az egyes lépések következetes végrehajtását.
- Ellenőrzés és mérés: A precíziós műszerekkel és metrológiai technikákkal végzett szigorú ellenőrzés és mérés igazolja, hogy az alkatrészek megfelelnek a megadott tűréseknek és minőségi szabványoknak.
- Kalibráció: A megmunkáló berendezések és mérőműszerek rendszeres kalibrálása elengedhetetlen a pontosság és a nyomon követhetőség megőrzéséhez.
- Anyagellenőrzés: Az anyag tulajdonságainak, összetételének és minőségének ellenőrzése kritikus fontosságú annak biztosításához, hogy a felhasznált anyag megfeleljen a tervezési követelményeknek.
- Munkavállalói képzés: A gépészek és a minőségellenőrző személyzet képzési és készségfejlesztő programok biztosítják, hogy jártasak legyenek szerepeikben és felelősségükben.
- Kiváltó okok elemzése: Ha nem megfelelő alkatrészeket azonosítanak, alapvető ok-elemzést végeznek a probléma forrásának meghatározására és a korrekciós intézkedések végrehajtására.
- Folyamatos Fejlesztés: A folyamatos fejlesztés kultúrája elősegíti az innovációt, és folyamatos fejlesztéseket hajt végre a megmunkálási folyamatokban és a minőség-ellenőrzési eljárásokban.
- Customer Feedback: A vásárlói visszajelzések összegyűjtése és elemzése segít azonosítani a fejlesztendő területeket, és összehangolja a megmunkálási folyamatokat az ügyfelek elvárásaival.
Következtetés
A. A precíziós megmunkálás művészete és tudománya
A precíziós megmunkálás a művészet és a tudomány metszéspontjában áll, ahol a kreativitás, a készség és az innováció egyesülve olyan nagy pontosságú alkatrészeket állít elő, amelyek vezérlik az iparágakat és formálják a modern világot. Ez egyrészt művészeti ág, amely a nyersanyagokat kiváló mérnöki alkotásokká alakító gépészek mesterségbeli tudását és szakértelmét igényli, másrészt egy olyan tudomány, amely a csúcstechnológiára, az anyagtudományra és a fejlett eljárásokra támaszkodik a páratlan precizitás elérése érdekében. A precíziós megmunkálás útja az anyagok és tulajdonságaik megismerésén, a forgácsolószerszámok és gépek elsajátításán, valamint a folyamatok és tűrések aprólékos ellenőrzésén keresztül vezet bennünket. Magába foglalja a geometriai méretezés és tolerancia nyelvezetét, a statisztikai folyamatszabályozás éberségét és a minőségbiztosítás iránti elkötelezettséget. A precíziós megmunkálás kulcsfontosságú szerepet játszik a különböző iparágakban, a repülőgépipartól és az autóipartól az orvostechnikai eszközökig és az elektronikáig, és mindent formál a repülőgép-hajtóművektől a mesterséges kötésekig és a mikrochipekig. Lehetővé teszi olyan komponensek létrehozását, amelyek páratlan pontossággal és megbízhatósággal működnek, gyakran feszegetve a lehetséges határait.B. Végső gondolatok
Ahogy a precíziós megmunkálás ezen feltárását befejezzük, világos, hogy ez a terület nem csak az alkatrészek létrehozásáról szól; a lehetőségek megteremtéséről szól. A precizitásra való törekvés ösztönzi az innovációt, feszegetve az elérhető határokat. Legyen szó az óra bonyolult fogaskerekeinek létrehozásához szükséges finom kivitelezésről vagy az összetett repülőgép-alkatrészek gyártásához szükséges fejlett technológiáról, a precíziós megmunkálás mindennek a középpontjában áll. A precíziós megmunkálás jövője tele van ígéretekkel. Az anyagtudomány, az automatizálás és a digitális technológiák fejlődése továbbra is átformálja a tájat. A miniatürizálás, a 3D nyomtatás és a fenntartható gyártási gyakorlatok egyre előtérbe kerülnek, és új távlatokat nyitnak meg az ipar számára. Egy olyan világban, ahol a pontosság minden eddiginél fontosabb, a precíziós megmunkálás továbbra is a modern mérnöki munka nélkülözhetetlen pillére. Az emberi találékonyságról és a gyártás minden területén a kiválóságra való töretlen törekvésünkről tanúskodik. A nagyobb pontosságú és bonyolultabb alkatrészek iránti kereslet növekedésével a precíziós megmunkálás tovább fejlődik, és ugyanazzal az elhivatottsággal és pontossággal felel meg a holnap kihívásainak, mint amilyeneket évszázadok óta meghatároztak.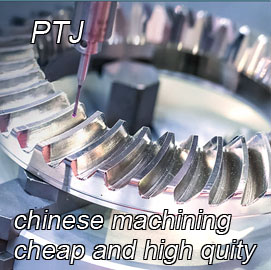
Szolgáltatásaink
- 5 tengelyes megmunkálás
- CNC-marás
- CNC esztergálás
- Megmunkáló iparágak
- Megmunkálási folyamat
- Felületkezelés
- Fém megmunkálás
- Műanyag megmunkálás
- Por kohászat penész
- Die Casting
- Alkatrészek Galéria
Esettanulmányok
- Autó fém alkatrészek
- Gépalkatrészek
- LED hűtőborda
- Épület alkatrészek
- Mobil alkatrészek
- Orvosi alkatrészek
- Elektronikus részek
- Személyre szabott megmunkálás
- Kerékpár alkatrészek
Anyaglista
- Alumínium megmunkálás
- Titán megmunkálás
- Rozsdamentes acél megmunkálás
- Réz megmunkálása
- Sárgaréz megmunkálás
- Szuperötvözet megmunkálás
- Kukucskáló megmunkálás
- UHMW megmunkálás
- Egyedi megmunkálás
- PA6 megmunkálás
- PPS megmunkálás
- Teflon megmunkálás
- Inconel megmunkálás
- Szerszámacél megmunkálása
- Több anyag
Alkatrészek Galéria